H13鋼自研發(fā)以來(lái),由于其優(yōu)異的力學(xué)性能(高強(qiáng)度、紅硬性、高韌性和良好的塑性)和較高的淬透性、中溫穩(wěn)定性等,被廣泛研究和應(yīng)用,常用作熱擠壓模具、高速精鍛模具、鋁合金壓鑄模具等。為提高H13鋼的使用性能和壽命,常對(duì)其進(jìn)行熱處理。
1 H13鋼的特性
H13鋼的國(guó)際標(biāo)準(zhǔn)化組織材料牌號(hào)為40CrMoV5,對(duì)應(yīng)不同國(guó)家的材料牌號(hào)見表1,其材料成分和物理性能見表2~表4 [1] 。H13鋼的熱處理臨界溫度見表5。
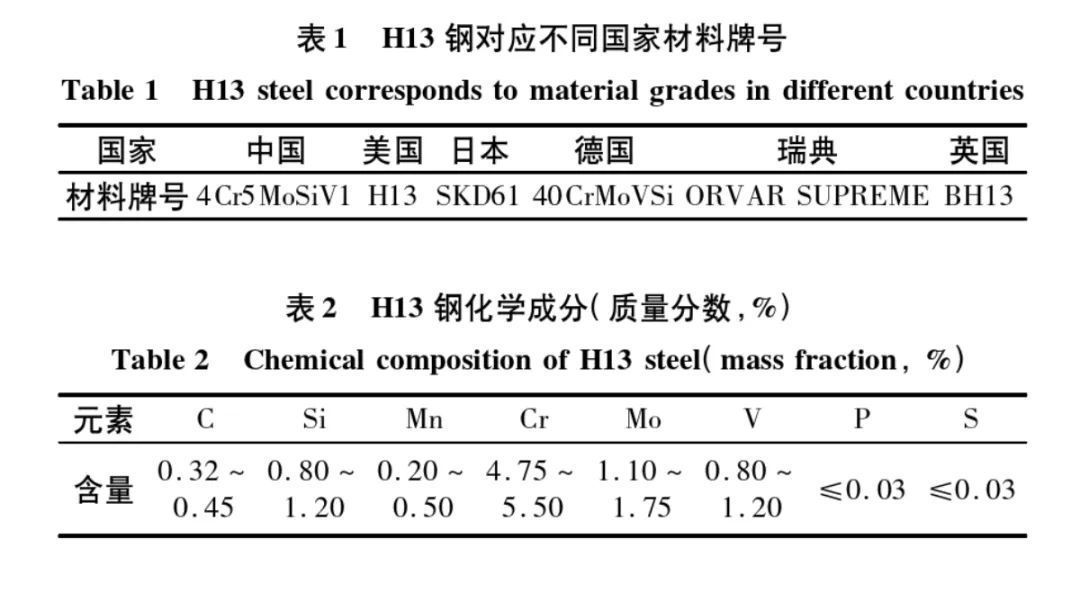

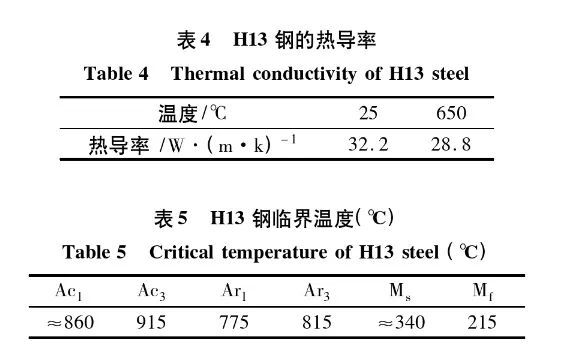
2 H13鋼常規(guī)熱處理工藝
H13鋼鍛后組織呈帶狀并通常含有粗大的一次碳化物,鍛后零件組織內(nèi)存在較大的內(nèi)應(yīng)力,對(duì)后續(xù)模具加工、服役和使用壽命均存在不利影響。為改善H13鋼的顯微組織和綜合性能,鍛造后需進(jìn)行適當(dāng)熱處理,進(jìn)而提升模具的綜合性能。
H13鋼常規(guī)熱處理工藝主要包括預(yù)備熱處理、淬火和回火,如圖1所示。
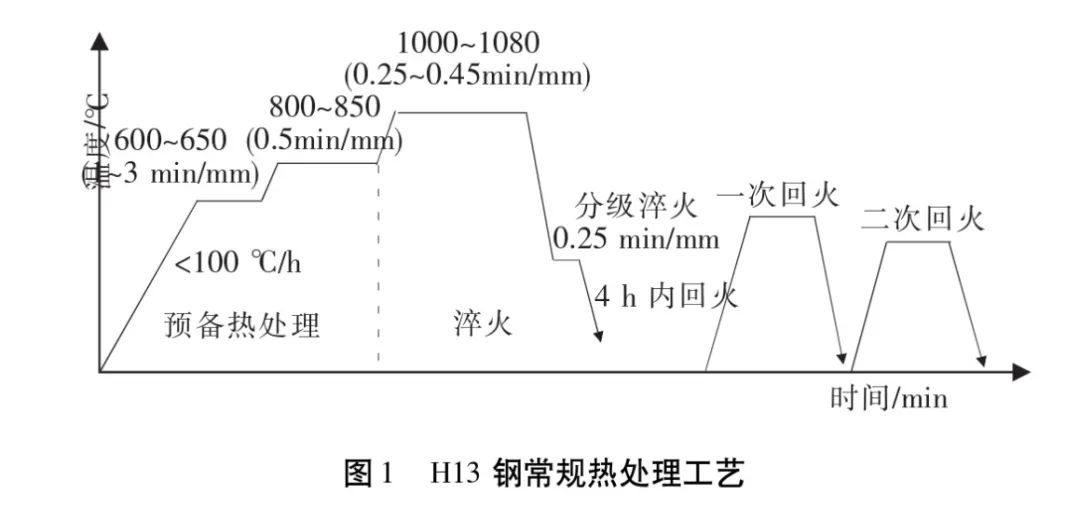
2.1 預(yù)備熱處理
H13鋼的預(yù)備熱處理工藝主要為退火或正火,有一次預(yù)熱、多次預(yù)熱等。預(yù)備熱處理工藝和預(yù)熱次數(shù)主要取決于鋼材尺寸大小和模具復(fù)雜程度,如去應(yīng)力退火+球化退火、正火+球化退火、雙級(jí)球化退火等,其目的主要是:①改善鋼材鍛后產(chǎn)生的帶狀組織,消除網(wǎng)狀碳化物 ,為球化組織和后續(xù)熱處理作組織準(zhǔn)備;②避免較快的加熱速度導(dǎo)致鋼材內(nèi)外部溫差太大,產(chǎn)生較大內(nèi)應(yīng)力,進(jìn)而引起嚴(yán)重的變形或?qū)е潞罄m(xù)淬火裂紋。
H13鋼碳含量為0.35%~0.45%,含有8%左右的合金元素,導(dǎo)致合金共析點(diǎn)左移,屬于過(guò)共析鋼。過(guò)共析鋼在淬火前,為了消除網(wǎng)狀碳化物,常在其Ac1溫度附近進(jìn)行球化退火,或在Ac1~Ac3溫度之間進(jìn)行不完全退火。H13鋼預(yù)備熱處理退火溫度一般選擇600~650 ℃,球化退火溫度800~850 ℃。第一階段較低的預(yù)熱溫度,可有效去除工件因前期加工產(chǎn)生的應(yīng)力,防止后續(xù)加熱導(dǎo)致的工件嚴(yán)重畸變,進(jìn)而造成開裂;也可以加快工件相變重結(jié)晶的加熱速度,使厚大工件內(nèi)外部溫度均勻時(shí)間縮短,大截面上奧氏體晶粒分布更加均勻細(xì)小,從而提高整體熱后性能。但過(guò)高的溫度可能導(dǎo)致后續(xù)回火時(shí)晶粒長(zhǎng)大或碳化物聚集球化,從而使工件脆性增大。第二階段較高的預(yù)熱溫度,可使碳化物大量析出并分段球化,此過(guò)程細(xì)小碳化物彌散程度更高,也避免過(guò)高溫度下導(dǎo)致的熱應(yīng)力和晶粒長(zhǎng)大。
張文莉等對(duì)H13鋼分別進(jìn)行“鍛造+正火+球化退火”和 “鍛造+球化退火”工藝,結(jié)果表明:鍛造后正火、球化退火對(duì)奧氏體中析出的碳化物形態(tài)和分布有改善作用,進(jìn)而影響力學(xué)性能表現(xiàn)。
鄒安全等 對(duì)H13鋼鍛件進(jìn)行常規(guī)退火(840~890) ℃×(2~4) h和等溫球化退火(840~890) ℃×(2~4) h后爐冷至710~740 ℃保溫3~4 h再爐冷至500 ℃以下出爐空冷,然后對(duì)試塊進(jìn)行淬火和兩次回火,結(jié)果表明:等溫球化退火后,H13鋼內(nèi)部可獲得球狀珠光體和彌散分布的粒狀碳化物組織,球化退火后的再次預(yù)熱也可提高碳化物彌散程度,為淬火后組織轉(zhuǎn)變提供了核心。
2.2 淬火
2.2.1 常規(guī)淬火工藝
通過(guò)各合金元素的固溶作用,淬火后組織內(nèi)包含大量淬火馬氏體和殘余奧氏體,能夠顯著提高H13鋼的強(qiáng)硬度和耐磨性,因而H13鋼一般需進(jìn)行淬火處理。固溶保溫時(shí)間一般根據(jù)H13鋼尺寸大小和模具復(fù)雜程度決定,通常選0.25~0.45 min/mm。固溶溫度一般選擇1000~1100 ℃,該溫度主要由基體內(nèi)相的熔點(diǎn)決定。有研究表明,超過(guò)1100 ℃時(shí),較高的溫度為組織提供了足夠的長(zhǎng)大激活能,奧氏體晶粒將明顯粗化,甚至產(chǎn)生過(guò)燒。淬火溫度一般選擇1000~1080 ℃。淬火溫度較高時(shí),馬氏體中的碳和合金元素含量升高,過(guò)飽和碳原子以間隙式溶解于馬氏體中引起強(qiáng)烈的點(diǎn)陣畸變導(dǎo)致畸變能升高,碳原子與位錯(cuò)纏結(jié),對(duì)馬氏體起到顯著的固溶強(qiáng)化作用,淬火后硬度較高。另外,淬火溫度較高時(shí),淬火組織中殘余奧氏體含量增加,殘余奧氏體分布在板條馬氏體之間起到阻礙裂紋擴(kuò)展的作用,提高了沖擊韌性。因此,為了獲得熱后較高的紅硬性,淬火溫度一般選擇上限溫度;為了獲得較好的韌性,淬火時(shí)采用下限溫度。
李勇等對(duì)H13鋼分別在650 ℃和850 ℃預(yù)熱30 min后,在1020~1080 ℃奧氏體化保溫5~7 min后油淬,結(jié)果表明:隨淬火溫度升高,硬度先升高后下降,在1050 ℃淬火時(shí)硬度最高,達(dá)到53 HRC。胡志剛 對(duì)H13鋼在550 ℃和800 ℃兩級(jí)預(yù)熱后,分別在1030、1070和1100 ℃溫度下淬火,保溫后進(jìn)行油冷及600 ℃回火,結(jié)果表明:淬火溫度提升后可以提高H13鋼室溫和高溫下的熱疲勞性能。
為了減少淬火組織應(yīng)力,H13鋼常進(jìn)行分級(jí)淬火,即先將鋼材在Ms溫度以上進(jìn)行鹽浴淬火,保持淬火液溫度一段時(shí)間后將鋼材取出,再在空氣中進(jìn)行冷卻。分級(jí)淬火可以獲得一定的淬火冷卻速度,在基體中保留高固溶度的合金組織,防止晶間碳化物過(guò)量析出;另外,降低了直接快速降溫至室溫時(shí)鋼材內(nèi)外冷熱收縮不一致產(chǎn)生的淬火應(yīng)力,工件內(nèi)部及外表面可以同時(shí)進(jìn)行馬氏體轉(zhuǎn)變,并減少下貝氏體的生成量,減少模具外形尺寸的快速收縮,防止淬火后變形開裂。
目前,除普通鹽浴爐之外,淬火冷卻過(guò)程也大量應(yīng)用真空爐。真空爐淬火是指整個(gè)淬火過(guò)程在真空爐內(nèi)進(jìn)行,將淬火介質(zhì)(如高純氮?dú)?送入真空爐內(nèi),通過(guò)控制氣體的流量和溫度來(lái)控制冷卻速度,熱效率較高,既可實(shí)現(xiàn)快速升溫和降溫,又可實(shí)現(xiàn)緩慢加熱以減少工件內(nèi)應(yīng)力,溫度控制嚴(yán)格且精確,淬火后工件表面無(wú)氧化、無(wú)脫碳和無(wú)氫脆等缺陷。且自動(dòng)化程度高,得到廣泛應(yīng)用。
除此之外,生產(chǎn)中還應(yīng)用流動(dòng)粒子爐進(jìn)行淬火冷卻。即在特定設(shè)備中用可燃?xì)怏w產(chǎn)生熱量,利用剛玉砂、石英砂、碳化硅砂等流動(dòng)的粒子流的不斷運(yùn)動(dòng)進(jìn)行熱交換和傳熱加速,從而對(duì)工件完成冷卻過(guò)程。整個(gè)過(guò)程爐溫可控、升溫速度快、環(huán)境污染小,工件也不會(huì)發(fā)生脫碳、氧化等現(xiàn)象,可以實(shí)現(xiàn)連續(xù)淬火,淬火后也可以直接進(jìn)行模具發(fā)藍(lán)處理。
馮英育等對(duì)大、中、小三種不同尺寸的H13鋼模具進(jìn)行單級(jí)鹽浴淬火、雙級(jí)鹽浴淬火、真空分級(jí)淬火和流態(tài)化床淬火,分析不同淬火方法下試塊的硬度和組織,試驗(yàn)最終表明:雙級(jí)淬火的第一級(jí)冷卻保溫時(shí)間應(yīng)當(dāng)足夠長(zhǎng)以保證模具表面和中心溫度均勻一致,組織轉(zhuǎn)變不會(huì)在恒溫過(guò)程中發(fā)生,因而可以適當(dāng)延長(zhǎng)第一級(jí)冷卻保溫時(shí)間以使鋼中貝氏體量盡量少,建議H13鋼第一級(jí)冷卻溫度大約為520 ℃,第二級(jí)冷卻溫度大約為200 ℃。
淬火后鋼材內(nèi)部一般存在較大的內(nèi)應(yīng)力,需要進(jìn)行適當(dāng)回火?;鼗鹂杀M量降低組織內(nèi)應(yīng)力,使其趨于平衡,避免后續(xù)因組織轉(zhuǎn)變?cè)斐赡>咄庑纬叽绲妮^大改變;還可將鋼內(nèi)殘余奧氏體繼續(xù)轉(zhuǎn)變?yōu)轳R氏體組織,在保證韌性提高的情況下不降低硬度。
H13鋼的回火工藝一般選擇500~650 ℃高溫回火。此溫度內(nèi)一般會(huì)發(fā)生H13鋼的二次硬化,殘余奧氏體轉(zhuǎn)變?yōu)轳R氏體的同時(shí),回火馬氏體中析出細(xì)密碳化物顆粒產(chǎn)生二次硬化,工件硬度重新升高至淬火時(shí)水平,鋼材殘余應(yīng)力減小。
寧鞍鋼等對(duì)鍛后H13鋼進(jìn)行860 ℃球化退火、1030 ℃淬火保溫30 min后油冷、590 ℃回火保溫2 h后油冷,對(duì)回火態(tài)H13鋼碳化物種類進(jìn)行分析和熱力學(xué)計(jì)算,統(tǒng)計(jì)不同部位碳化物析出尺寸和數(shù)量,結(jié)果表明:H13鋼回火態(tài)主要析出富V元素的MC碳化物、富Mo元素的M2C碳化物(<200 nm)和富Cr元素的M23C6碳化物(>200 nm),其中前兩者主要沉淀強(qiáng)化作用,在1/2R處析出最多,表面最少。
由于一次回火后殘余奧氏體未發(fā)生全部轉(zhuǎn)變,為進(jìn)一步提高材料的性能,常進(jìn)行二次回火,甚至多次回火,使組織中析出更多細(xì)小彌散的強(qiáng)化相提高其整體性能。
3 其他熱處理技術(shù)
3.1 氮化處理和氮碳共滲
氮化處理和氮碳共滲可顯著提高H13模具鋼的疲勞強(qiáng)度、耐磨性和耐蝕性,具有滲氮速度快、滲氮層性能好的優(yōu)點(diǎn)。生產(chǎn)中應(yīng)用非常廣泛,常應(yīng)用在模具加工完成之后。
趙昌盛等對(duì)H13模具鋼進(jìn)行雙級(jí)預(yù)熱+1030 ℃淬火+600 ℃回火后,再進(jìn)行580 ℃×4.5 h氣體氮碳共滲,油冷,得到氮碳共滲層厚度約0.20 mm,模具表面硬度達(dá)到900 HV以上。氣體氮碳共滲相當(dāng)于模具淬火、加工后的一次回火,模具壽命是常規(guī)熱處理的2倍以上。
鄭小燕等對(duì)H13鋼進(jìn)行1050 ℃淬火+560~600 ℃兩次回火處理后,再進(jìn)行540~570 ℃×12 h離子滲氮,得到表面滲層厚度0.24 mm,白亮層約10 μm, 硬度約67 HRC,模具表面耐磨性和壽命得到一定提升。
近年來(lái),激光處理因其工作效率高、強(qiáng)化層深、無(wú)污染等優(yōu)點(diǎn)受到各行業(yè)廣泛的關(guān)注和研究。
葉四友等對(duì)H13鋼表面進(jìn)行激光熔覆H13合金涂層,激光功率為1.4 kW,掃描速度為14 mm/min,送粉速率為42 g/min,涂層的截面顯微硬度達(dá)到669~698 HV,為H13基體的2.85~3倍。
陳峰等在H13鋼表面激光熔覆Ni基合金涂層,結(jié)果表明:熔覆層截面顯微硬度平均高達(dá)800 HV,為基體的3~4倍。
李班等采用激光熔覆技術(shù)在H13基體表面制備了85%H13+15%Cr-3C-2NiCr粉末的復(fù)合熔覆層,熔覆層表面顯微硬度值接近1100 HV0.2,約為基體的2倍,實(shí)現(xiàn)了H13鋼的表面強(qiáng)化。
4 總結(jié)及展望
對(duì)H13鋼進(jìn)行分級(jí)預(yù)備熱處理、淬火后分級(jí)冷卻及多次回火可以獲得較高的綜合性能。
隨著社會(huì)的快速發(fā)展和科技制造水平不斷創(chuàng)新,H13鋼性能提升需求也日漸增大。如何更高效地發(fā)揮H13鋼的性能,提高其熱處理水平來(lái)滿足不斷發(fā)展的需求將是學(xué)者們繼續(xù)研究的方向。在傳統(tǒng)工藝上,更安全高效、自動(dòng)化水平更高、環(huán)境污染更小的熱處理強(qiáng)化方式將得到更廣泛的關(guān)注和研究。
來(lái)源:中國(guó)熱處理行業(yè)協(xié)會(huì)
免責(zé)聲明:本文系網(wǎng)絡(luò)轉(zhuǎn)載,版權(quán)歸原作者所有。僅標(biāo)明轉(zhuǎn)載來(lái)源,如標(biāo)錯(cuò)來(lái)源,涉及作品版權(quán)問(wèn)題,請(qǐng)與我們聯(lián)系,我們將在第一時(shí)間協(xié)商版權(quán)問(wèn)題或刪除內(nèi)容。內(nèi)容為原作者個(gè)人觀點(diǎn),并不代表本公眾號(hào)對(duì)其真實(shí)性負(fù)責(zé)。